Getting the team �on the bus� increases production for rendering plant
Article Index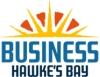
Growth in production throughput is one of the key benefits experienced by Hawke’s Bay Protein from its participation in a productivity programme, but perhaps of greater impact is the growth in confidence, communication and management skills gained by key supervisory staff.
When Shaq Gardner was promoted from the floor into a production manager position to assist general manager Bruce Rountree, he quickly realised he needed to be freed up from working in the factory that produces ovine meal for export markets. Instead he was continuously being pulled back to problem solve issues.
Good fortune smiled when he became aware of Glenn Manahi, from Hawke’s Bay business improvement firm Smarter, Better, Faster (SBF), and the High Performance Work Initiative offered by Business Hawke’s Bay in partnership with Hastings District Council and co-funded through Callaghan Innovation.
HB Protein is a 24/7, 365 day a year manufacturing plant employing 25, that renders unwanted stock parts from meat works (heads, hocks, etc) down to a dry meal. This is then exported predominantly to the European Union as an ingredient for domestic animal dry food. New Zealand lamb is considered a premium product and its inclusion is used as a selling point to European pet owners. Tallow by-product from the rendering process is exported to China for soaps and Singapore for bio-diesel.
In 2015, Lowe Corporation became a shareholder of HB Protein and, consequently, a significant increase in raw materials to be rendered came onstream. New equipment was purchased to handle the extra volume and Bruce Rountree recognised he needed to restructure his team to achieve better production levels; he promoted Shaq Gardner from supervisor and created new supervisor roles filled from the floor and from new recruits.
For the 19 years’ Bruce has headed Hawke’s Bay Protein he has found getting everyone to “sing from the same hymn sheet” problematic. There were many manufacturing and engineering issues, and too much variation in processes resulting in quality inconsistencies.
Now 12 months later, the HPWI programme has helped turn this around. The plant is cooking faster to keep current with the increased volume; production delays have dropped dramatically, which means that odour issues from raw materials have reduced, with a pleasing decrease in complaints from the plant’s neighbours. And importantly, product quality has improved.
For Shaq, the programme has seen the six supervisors who cover day, night and weekend 12 hour shifts all “on the same page”, and communication and morale within the business hugely improved. The ‘us’ and ‘them’ thinking prevalent in the past, is now replaced with a much happier, more relaxed and cohesive workforce.
“Where we are now, 12 months’ down the track, is very far from anything I could have imagined. We are hitting our goals that are set higher than ever before and already thinking we can be over and above these next year,” he says. “I don’t think I could be doing the job I am now without the programme and what it has helped us achieve.”
Under Glenn Manahi’s facilitation, the supervisory team mapped out the manufacturing process and identified the issues and roadblocks. It became very apparent there was variability in the way supervisors were supervising, there were limited Standard Operating Procedures and those in place were not being followed or consistently managed by supervisors or management.
The outcome of this investigative process was the establishment of a training programme for supervisors that established roles and responsibilities and identified ways to create a cultural change.
This included establishing an accepted supervisory style, setting standards, goals and targets, and required the full supervisory team to be “on the bus” with the change. All of this was then communicated by the supervisors to their respective teams, which for some was a huge challenge but once successfully accomplished, was a real boost to their confidence.
Each Monday evening, there is now a one-hour meeting for all supervisors to discuss issues, plans and generally share their collective skills and ideas to keep production on track. They review KPIs and agree on what needs to be done to keep hitting them.
In tandem with the supervisors’ training programme, a compliance officer has been employed and there is a succession plan in place to train up new supervisors.
The changed cultural environment has had the added spin-off of improving problem solving. A review of maintenance issues and subsequent collective brainstorming saw the full team identify 16 small to medium improvements that would improve safety, productivity, reliability and yield.
“We are asking people for their opinions and ideas and working together up and down the chain to make things better,” says Shaq.
Another unexpected benefit of the programme was the ability to network with other businesses involved in the High Performance Work Initiative, he says. “It’s been great to see that others are in the same boat and to hear how they came through the process and what they have learned.”
ENDS
Image caption: Shaq Gardiner, Hawke’s Bay Protein production manager has the initial mapping process up in his office to remind the team of what was identified and how far they have come in addressing the issues that were impeding productivity.